Mechanical systems:
Bearings:
Some of the most critical components in any industrial setting are bearings. Bearings are mechanical components used to reduce friction and provide load support for rotary or linear equipment. A single bearing failure can cause hours of downtime, including the identification and replacement of the failed component. Ultrasonic technology provides the ability to monitor and determine the conditions of bearings including:
- Good Condition: A roller bearing that is in good condition and is properly lubricated normally produces a soft whirring sound with very few, if any, crackles.
- Under-Lubricated: Inadequate lubrication produces a very intense scraping or squeaking sound.
- Over-Lubricated:Too much lubrication can cause no sound at all
- Damaged:Flat spots, scratches, or nicks on a bearing cause a grating, scraping, or clicking noise referred to as crackles.
CTRL's ultrasonic sensors can be used to check and recheck bearings at the very beginning to verify that installation is correct, and provide the earliest indication of defects.
In some cases, the bearing housing cannot be reached safely and an acoustic attachment must be used. Both the Mini-Concentrator and PowerBeam 300 are ideal because of their narrow beam of reception.
Normal bearing:SOUND
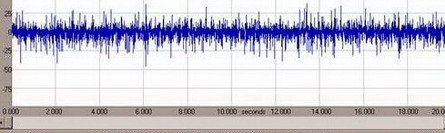
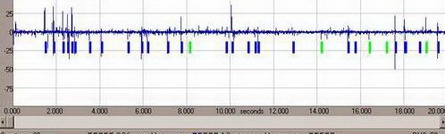
Gearboxes:
Teeth deformation and wear depend upon the type of sliding contact associated with the various types of gear sets. The operation of different types of gears emits a wide spectrum of airborne and structure-borne ultrasonic vibrations. Ultrasonic vibrations are the evidences of the operational conditions of the gears, as well as the rest of the transmission. The spectrum of ultrasound vibrations depends upon many design and operational features of the gear drive, namely.
When testing the gearbox, it is necessary to be familiar with the operating conditions and normal sounds produced. Using the UL101 in contact mode, listen to several points near specific components. The UL101 can be adjusted to distinguish the high-pitched sound of the input shaft. The output shaft may sound low and monotonous or low and have a natural clicking. It depends upon the type of gears and the load.
Valves:
A steam trap can fail open or fail closed. Traps that have failed open result in the loss of steam and energy. Water is also lost when condensate is not returned. Heating costs will rise and boiler plant costs rise significantly. When a trap fails closed, heating capacity is lost and damage can be done to the steam heating equipment.
By simply pressing the tip of the solid probe (attached to the UL101 receiver) against the steam trap, the user can easily hear the trap functioning and determine its operating condition. When it is difficult to reach a steam trap safely, the PowerBeam 300 can be used because of its ability to enhance the distance and narrow the reception of the UL101 Receiver. If the trap is working properly, the operator, using the UL101, can hear the rising of the valve and passing the rush of steam until closed. This indicates the valve is functioning properly. If the operator only hears silence or only hears steam rush/roar, the steam trap is either open or closed all the time. The operator will sometimes hear the trap close partially when it should close completely. This means that they will hear a tiny rush or drip, when they should hear silence. A steam trap that is not working properly is probably due to clogging or worn parts and needs to be cleaned or replaced.
Compressors:
Statistics show that the average air system wastes between 25% and 35% of its air due to leaks. A 1000 CFM compressed air system with a 30% leak rate costs an additional $45,000 per year to operate.1 The best way to maximize the cost of operation of running a compressor is to use ultrasound to minimize the number of air leaks in the system. Ultrasound can also be used to monitor the opening and closing of valves and pistons as well as determining the condition of the motor bearings.
When monitoring the opening and closing of valves or pistons of a compressor, it is necessary to use the UL101 in conjunction with the solid probes. Additionally, SoundCTRL can be used to record the ultrasonic output and zoom in on the waveform to see the individual cycles, providing better detail about its operation. Clogged or worn valves will have a distinct muffled sound compared to the crisp sounding impact of a new, clean valve. The use of the UL101 and the Concentrators or Acoustic Extension Probes is best suited for finding air leaks. It is best to start at the compressor and work out, along the air lines. In some instances, it is difficult to survey within 50 feet of the air line. Therefore, it is recommended that the PowerBeam 300 be used. The parabolic attachment can detect ultrasound from up to 300 feet away and pinpoint the source within one degree from center.